Animal feed serves a critical role in the global food sector by enabling cost-effective manufacturing of animal proteins all over the world. Feed is the most important and most significant component in providing safe, abundant, and economical animal proteins.
It is well known that the Indian animal feed market can be summarised into three basic categories: poultry feed, aqua feed and cattle feed. The poultry feed market has dominated the animal feed sector, accounting for over 44% of the global market.
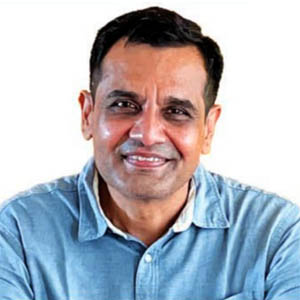
Managing Director – RKBFM
The manufacturing process of animal feed can be divided into various stages, with specialised feed processing equipment available at each stage. In this particular article we will discuss about animal feed grinding and feed particle size which is the initial stage of animal feed manufacturing.
Feed particle size is one of the most overlooked aspects of poultry production.
Animal feed grinding can be broadly categorized in two major categories:-
- Coarse grinding – generally used in poultry feed
- Fine grinding – generally used in aqua feed
Though the basic principle of grinding is the same in all types of feed grinding, some of the process parameters, equipment design, etc. get changed as per the category.
Though it has been hypothesised that finer grinding increases substrate availability for enzymatic digestion, there is evidence that coarser grinding to a more uniform particle size improves the performance of the birds kept on mash or on pellet.
In this article, we cover coarse grinding, grinding equipment, their specific features & engineering data of poultry feed grinding.
COARSE GRINDING
Particle size is an important factor that determines feed efficiency and gut health in poultry. Generally, the mash particle size which gets pass through 2.5 mm (& more) hole perforated sieve, is considered as coarse grinding.
Coarse particles stimulate gizzard development, and a well-developed gizzard improves energy utilisation and the digestibility of nutrients and lowers the pH value of the digested material. Coarse grinding also saves energy and time in the grinding process. On the other hand, it is well known that pelleting reduces the size of the microparticles that make up the pellets, but coarser grinding prior to pelleting is expected to increase the proportion of coarse particles in the pellets to some extent, which will promote stomach development.
GRINDING UNIT OF THE FEED MILL
To achieve effective grinding, a hammer mill alone is not sufficient. The supporting system has a great role in achieving the best throughput from the hammer mill. It is common practice to refer to the grinding unit as a hammer mill alone, but it is the entire grinding station comprise of:
a) Hammer mill
b) Aspiration unit
c) Plenum chamber
Some elaboration along with engineering data and parameters on the above component of grinding station is as follows:
• a) Hammer mill: A hammer mill is one of the key machines of feed mill. Optimum throughput and perfect particle size are the two factors that define the quality of hammer mill operation. A hammer mill should be designed & manufactured with the utmost care and the following points should be maintained:
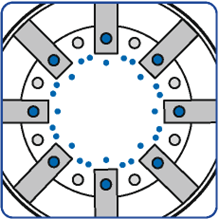
-
- Sturdy, Heavy-weight base for minimising vibration.
- Sliding or rotating doors for better accessibility of the rotor.
- Doors with door safety switches & zero speed sensors to avoid any human accident.
- A specially designed rotor having plug – in / plug – out type beater holding arm assembly.
- Double hole concept (dual hammer position) in rotor plates for increasing/decreasing the distance between beater and sieve as per the requirement of fineness of powder.
- Sieve perforation: For poultry feed milling, 2.5/3.0/3.5 mm perforations are being used in the industry depending upon the raw material used.
- Hammer mill beater – A hammer mill beater’s function is to smash and grind materials that are supplied into the hammer mill. The beaters strike the material as the shaft rotates, breaking it down into smaller particles. The hammer mill beater is the most significant component because it performs the majority of the grinding operation.
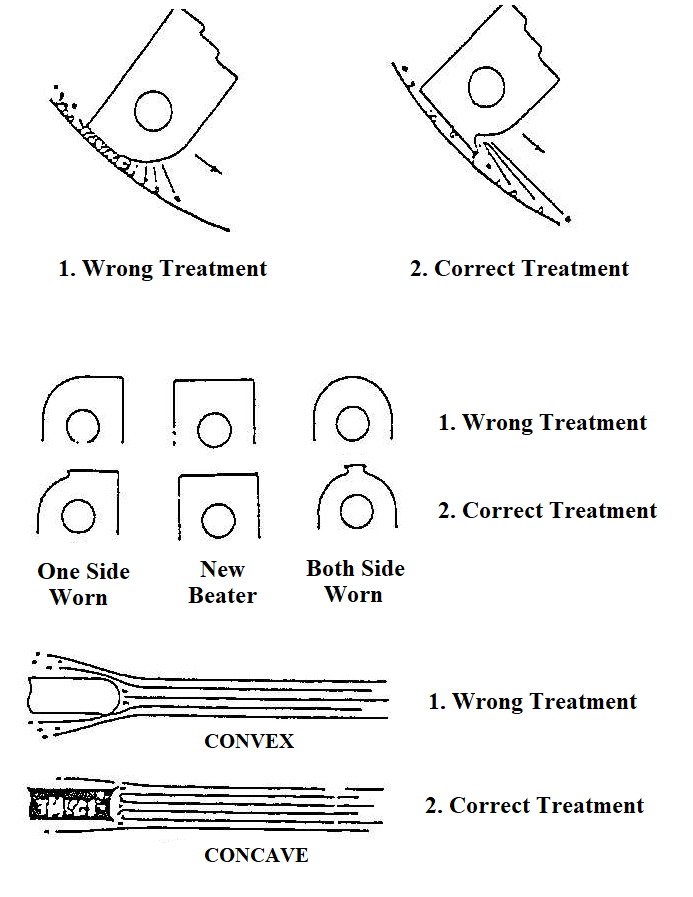
-
-
- Hammer mill rotor speed – Unlike previous type of power transmission through belt-pulley arrangement, now a days direct drive through coupling is the preferred design.
For poultry feed milling, Hammer mills directly coupled with high rpm (2600-3000) motor with smaller diameter rotor and hammer mills directly coupled with Low rpm (1200-1500) motor with larger diameter rotor (to keep the same tip speed) are being used. VFD operated mill can be used to run the motor at lower rpm.
- Hammer mill rotor speed – Unlike previous type of power transmission through belt-pulley arrangement, now a days direct drive through coupling is the preferred design.
-
- b) Aspiration unit: The right kind of aspiration unit with a sufficiently large plenum chamber is the back bone of the grinding station. The effectiveness of the aspiration unit ensures the cleaning of perforations of the hammer mill Sieve, which is directly proportional to get more output from hammer mill, less jamming & better current control of hammer mill motor.
Design of aspiration system needs the following factors:
-
- Size of the blower (Air flow rate and air pressure)
- Surface area of the filtering media
Following is the engineering data on the above
a) Airflow through hammer mill screen – 8300 to 8500 m3/hr per square meter of screen area.
b) Differential air pressure across the system – 300 to 500 mm water column.
c) Surface area of the filtering media – 120 to 130 m3/hr of air per square meter cloth.
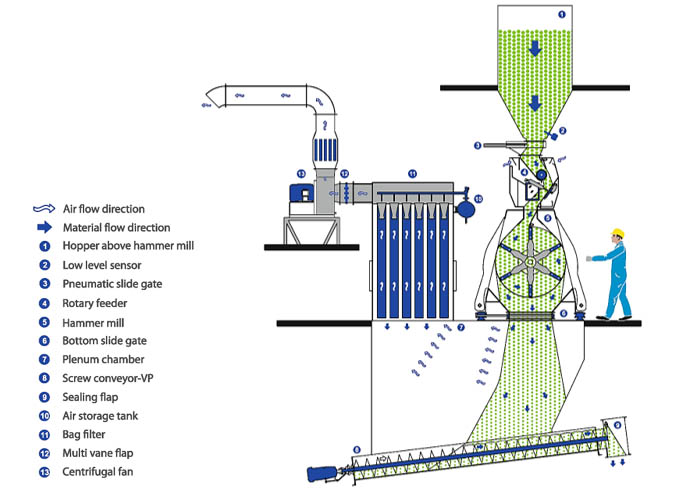
- c) Plenum chamber: Generally, least importance is given to volume of the plenum chamber and consider it a transition piece. The size of the plenum chamber should be large enough to provide space for air circulation generated by hammer mill rotor. In absence of the space for air circulation, the air gets trapped in the grinding chamber. It may cause the hindrance in letting the raw material into the grinding chamber from the hammer mill feeder or overloading the filtering media, resulting in increase in pressure drop across the system.
We at RKBFM are putting our constant efforts to improve the design of the feed mill machines. We are attempting to share what we know and have gained over the course of more than 25 years of experience.
We welcome and appreciate if you can send us the topics of your interests. We will try to include your requests in future publications. You may send your topic suggestions at info@Poultrytrends.in
In our next article, we will briefly discuss the next step of animal feed manufacturing process.
Since inception, RKBFM has been continuously contributing towards the development of innovative designs thus generating lasting value for its clients. We possess the capability to deliver a wide range of animal feed, wood and biomass pellet plants and our experience of over 25 years in this field enable us to manufacture top quality products. Over the years, we have expanded our reach across the world including Nigeria, Malawi, Egypt, Uganda, Kenya in African region for feed plant, machines and its spares.
We commit ourselves to provide the best solutions in design, manufacturing and supply of world class feed plants, machinery and spares by leveraging our expertise, proprietary information and ingenuity to enhance the business performance of our clients. At RKBFM we value the unique requirements of every client and thus believing in investing time in understanding the client’s needs.
To know more about us, you can visit our website www.rkbfm.com
Author: Mr. Deepak Bhandari, Managing Director – RKBFM